Introduction
Modern technology continues to change business landscapes at pace, not least in the manufacturing industry. If your organisation is looking for an edge, the clue is in the title. Edge computing applications in manufacturing could be the key to transforming productivity and profitability over the years to come.
In this guide, we’ll look at edge computing manufacturing use cases, benefits, and challenges while also considering future trends to help you get the most out of your applications. Let’s get started.
What is Edge Computing?
Edge computing is defined by Cloudflare as a “networking philosophy focused on bringing computing as close to the source of data as possible in order to reduce latency and bandwidth use”. By using the Internet of Things (IoT) devices and web applications to bring computers closer to data sources, fewer processes are required and long-distance communications between servers and clients are significantly reduced.
The networking technologies can be used across a wide range of business sectors and environments. However, edge computing in the manufacturing industry focuses largely on bringing computing resources closer to production lines with a view to analysing data and making quick, data-driven decisions relating to machinery or processes.
Computing resources could be used to monitor virtually any machine on the production line, from lathes and milling equipment to packaging machinery. As well as using PCs to bring computing closer to data sources, businesses can use Opto 22 products like groov RIO or groov EPIC to get OT data onto premises or cloud applications.
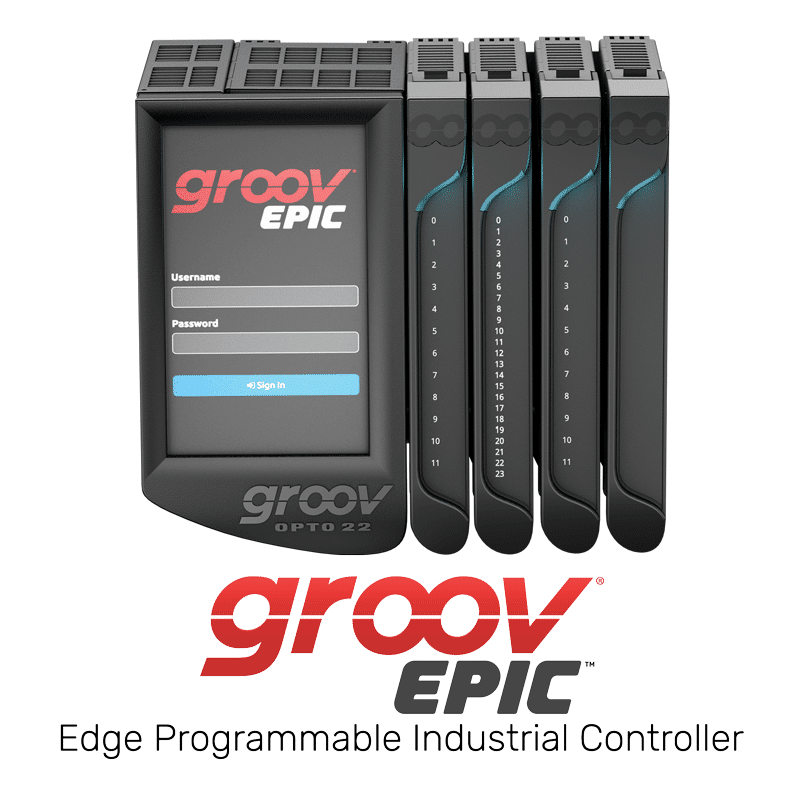
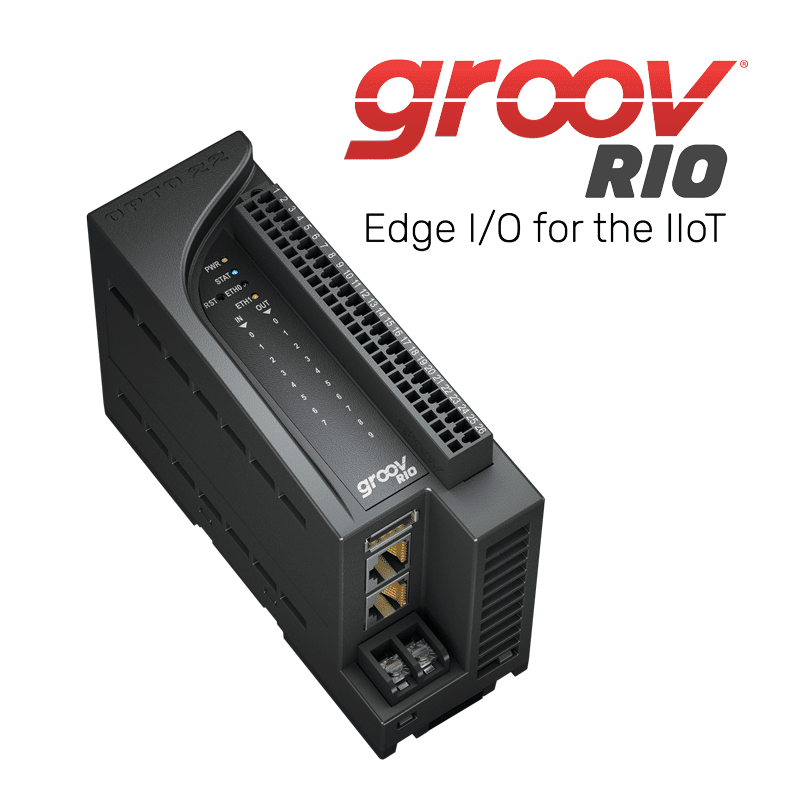
5 Benefits of Edge Computing in Manufacturing
Edge computing delivers a range of benefits for businesses across all sectors, such as low latency (meaning greater quality control for real-time data) and increased data security. It is particularly important as data breaches cost Australian firms an average of $3.35 million per breach. You will also find that it saves money if working with large volumes of data as sending this to the cloud costs money for data storage.
However, edge computing in manufacturing delivers several industry-specific benefits too. They include but are not limited to:
- Raw data filtering: Data filtering allows the company to only store relevant, contextualised data in the cloud. This supports cost-efficiency while also enhancing data analysis for on-site teams and off-site teams alike.
- Problem alerts: Undisrupted connectivity is particularly vital in manufacturing where machinery is very expensive. It ensures that any relevant alerts come through immediately, allowing teams to take the appropriate corrective action.
- Defect prevention: Connectivity also means time-sensitive applications will not suffer defects due to lost data recording. It will support the accuracy of all data-driven decisions and could potentially protect machinery.
- Faster decision-making: Having data analytics available with real-time results at source supports employees by allowing them to make quick, data-driven decisions with autonomy and 100% confidence.
- Machinery support: Some legacy applications within the manufacturing arena are simply not designed to run in the cloud. Edge computing enables manufacturing plants to maintain optimised performances across all equipment and processes.
Additionally, integrating edge computing devices such as groov RIO or groov EPIC into your network is straightforward, providing your team with complete flexibility and scalability.
Key Applications in the Manufacturing Industry:
Edge computing in manufacturing can support daily and ongoing operations in several ways. Therefore, defining the intended applications is an essential precursor to deployment, configuration, and monitoring.
Each company is unique and must find the applications that work for them, but the most common edge computing use cases in manufacturing are;
- Predictive Maintenance: Edge computing for manufacturing systems can track data relating to machine performances. The real-time analytics can identify and schedule maintenance, thus avoiding unscheduled downtime. Given that this costs Australian businesses up to $349,000 per hour, overcoming this is vital.
- AR/VR: Augmented Reality and Virtual Reality are beginning to play key roles in manufacturing plants. Edge computing provides valuable data for training, safety, and efficiency. Low latency also improves the experience of using this type of tech, thus supporting any employee who needs to use it.
- AI/ML: Artificial Intelligence and Machine Learning are also crucial ingredients in the recipe for smarter decision-making processes. Edge computing collects and aggregates data while also reducing the need to process all data in the cloud. AI and ML systems can subsequently develop faster and deliver more value to plants.
- Customer Services: Every new tech feature should ultimately enhance customer experiences. Edge computing brings versatility to data management, allowing teams to adjust manufacturing practices based on changing client behaviours and trends, thus remaining ahead of the curve and able to maintain customer satisfaction.
- Automation: Manufacturing is moving towards automation, as is shown by autonomous factories. Even if you don’t intend to operate without human agents, the use of automation can speed up processes and boost accuracy. Edge computing uses real-time data to facilitate automated assignments in style.
Overcoming Challenges with Edge Technology
Edge computing technology can help modernise manufacturing plants by streamlining data collection and analysis while also influencing staff morale. Better still, Opto22 tools support lean manufacturing to cover all equipment and sectors within the manufacturing arena.
While it is a useful addition for any of the 100,000+ manufacturing businesses in Australia, there are several obstacles that must be considered. The main issues, along with their solutions, include;
- Network demands: Data transmissions within the premises will place a lot of strain on the local network. Thankfully, investing in high-quality networking infrastructure can prevent this from becoming an issue.
- Management: While individual nodes and hardware can be managed with ease, managing the entire network can prove difficult. Not least because you need to prevent duplicate data or conflicting data. The right setups solve this issue.
- Costs: Introducing edge computing for manufacturing purposes requires an initial outlay while upscaling demands additional hardware purchases. Partnering with Binford Tech helps you get the best prices and achieve a truly tailored solution.
- Single point of failure: If opting for centralised edge computing in manufacturing plants, there is an added threat of a potential single point of failure. Opting for alternative edge solutions stops this, although quick resolution plans are ideal too.
- Contextualising data: Ultimately, edge computing use cases in manufacturing settings rely on the ability of employees to extrapolate meaning from data. Staff training and suitable planning before adding edge computing systems is vital.
With the right preparations and management, the potential downsides of edge computing in manufacturing are largely removed. However, the development of winning strategies has to start from the top and filter down throughout the business.
Future Trends in Manufacturing Technology
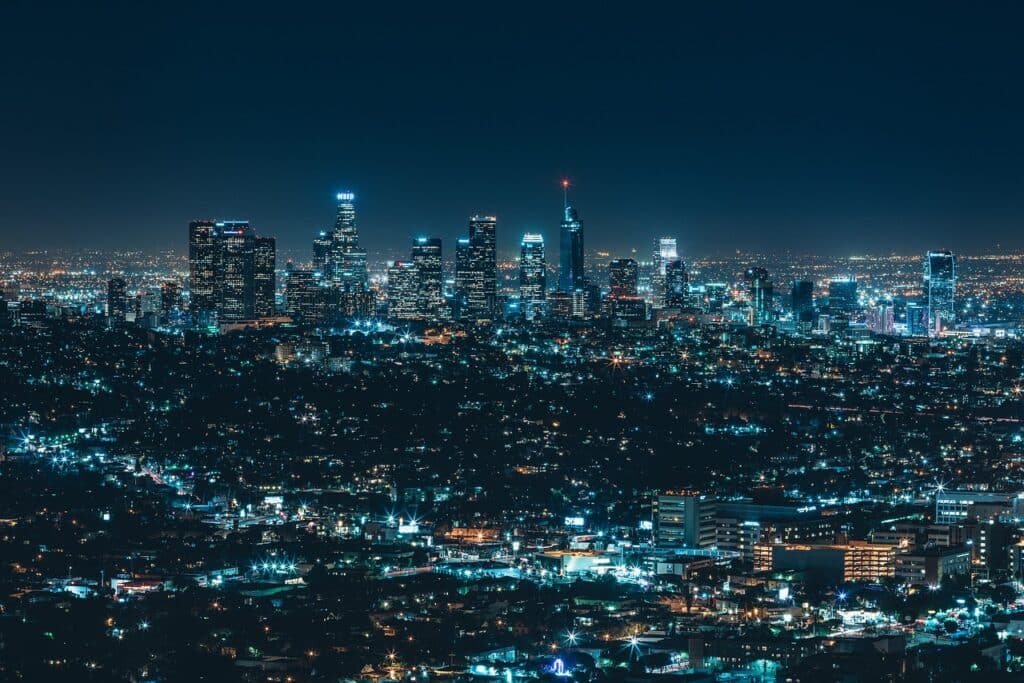
Effective edge computing isn’t simply about thinking about today’s needs. It must also align with your overall strategy while simultaneously establishing a platform from which you can build sustained success. Therefore, understanding the latest and upcoming trends is vital, not least because edge computing currently shows a CAGR of 33.6%.
Some of the key trends to consider for the rest of 2024 and beyond are;
- Edge AI: Artificial Intelligence continues to play an increasingly important role in business. Edge AI allows for automated decision-making based on the data harvested from having computer resources close to data sources. This creates streamlined, dynamic manufacturing plants.
- 5G: While connectivity to the cloud may be less demanding, edge computing IoT technologies still need fast connections. 5G technology takes speed and consistency to new heights, thus reducing any latency. As such, the demand for 5G edge cloud infrastructure is sure to grow.
- Blockchain: Increased security is a key selling point for edge computing, not least in the manufacturing industry. Blockchain tech creates data records that cannot be infiltrated or counterfeited while sensitive data cannot be traced back or attributed to its source. The extra layer of protection is ideal.
- Fog Computing: Fog computing processes data in a decentralised way, supporting both latency and bandwidth requirements. It also aids efficiency and scalability by removing the dependence on centralised cloud systems. A lot of companies will focus on fog computing, especially ahead of expansions.
- IoT: The Internet of Things supports interconnectivity for smooth data interactions between manufacturing equipment to build complete data models. As IoT continues to grow in popularity throughout organisations, its presence in manufacturing edge computing setups is likely to follow suit.
How We Support Your Edge Computing Needs
By now, you are probably keen to embrace edge computing in IoT manufacturing. Here at Binford Tech, our experts have helped many companies like yours and can assist your through the tech transition too.
We are Australia’s official distributor for Opto 22 products, including both groov RIO and groov EPIC, to ensure that you have the hardware needed to implement edge computing with success. In addition to providing the industry leading hardware at the best prices, our experienced professionals are committed to supporting your business with a tailored solution.
Following a full consultation, we’ll help you choose the right edge computing hardware and guide you through implementation and integration with existing manufacturing or data collection features. In turn, you should be positioned to make the most of edge computing in manufacturing in the immediate and long-term future.
To learn more about Edge Computing, as well as its impact on Opto 22 products like groov RIO and groov EPIC, get in touch with us today.
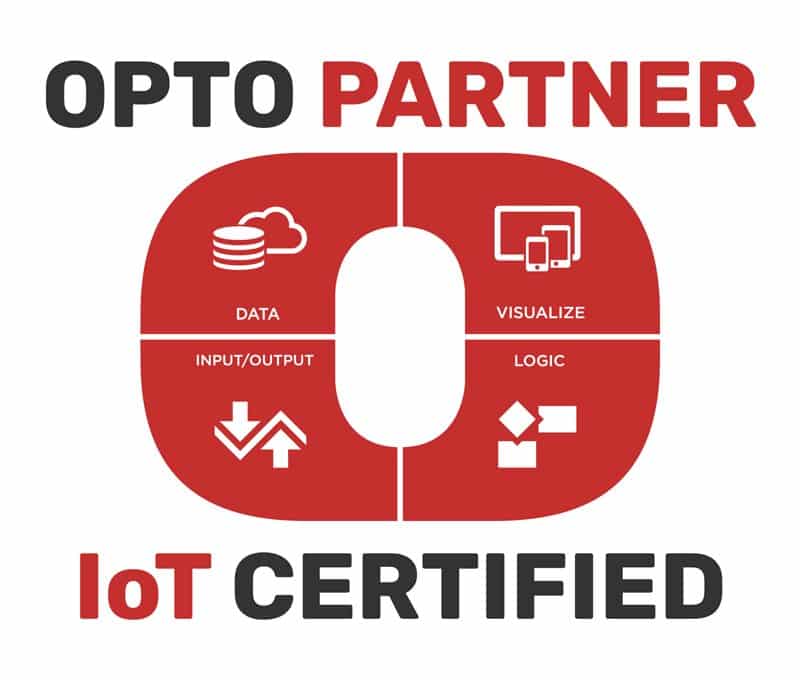